As soon as this one arrived, I knew I had to start on it at the earliest
opportunity. After clearing a few other projects off the bench, I started on
this one. I'll say from the beginning that one has to treat Kitty Hawk kits
as if they are short run. This means that parts cleanup may be a bit more
and that fit will require a lot of testing before applying cement to be sure
things will properly fit. If one takes it slow and easy, then there should
be few issues.
I discovered during construction that the parts
listed for the G sprue were actually on the E sprue and vice versa so you
may want to take this into consideration on your build.
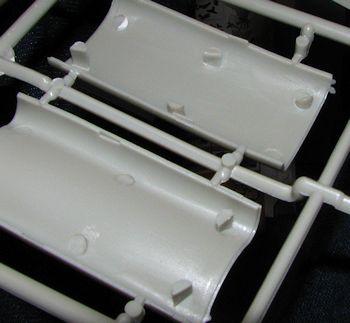
What I did was to start with the first sprue in the box. I know this is not
exactly according to the instructions, but looking them over, I saw that I
could get a bunch of subassemblies done before going back and following the
direction. The initial sprue has the intake trunking and the
vertical/horizontal stabs that can be done. The first thing I did was to
remove all the ejector towers from the first section of the intake. These
will be quite visible and so it is important that they are removed and the
many indentations filled. I used sprue cutters to get rid of most of the
towers and 220 grit sandpaper to smooth them down, after which, all the
indented areas got filler. The aft intake sections only had indented ejector
marks and was not filled. Once those were treated, they were painted
aluminum and assembled.
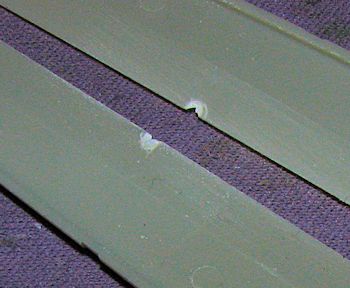
Wings and control surfaces.
I am also not a fan of the current trend to have sprue gates flush with
gluing surfaces. Not only do I tend to oversand when removing them, but if
not careful cutting them free, I'll take chunks out of the plastic. I had
this happen on the trailing edges of two of the horizontal stabilizer halves
and all eight of the aileron and flap halves. I also found two of them with
large, rather thick flash so care had to be taken when removing these items.
As I said, treat it like a short run kit. Eventually I got the divots
repaired and assembled the wing halves after filling in the inner
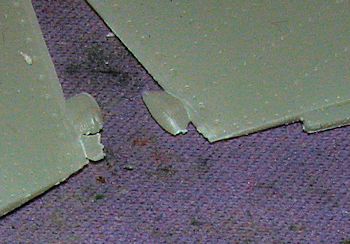
pylon holes. These items were
all set aside while I attended to other subassemblies.
The rocket well. This assembly consists of six parts. There are two small
items, C 8 and C 9 which fit into holes near the back of the well. The holes
for these needed to be opened up on my kit as they were flashed over. I also
snapped C 8 in half when sanding off the sprue attachment point. If I were
you, I'd also sand down the mating surface as the one that didn't break was
bowed when the assembly was done. The back wall piece, C 23 will not fit
flush in the center, but don't force it as when you attach the side walls,
everything will fit properly. This assembly was painted aluminum and set
aside.
Engine and exhaust. I started with the exhaust by first painting the inside
of most of the exhaust bits with Alclad II jet exhaust. The final compressor
stage was painted steel. This was then assembled. For the front of the
engine, the cone was painted dark aluminum as was the first compressor
stage.
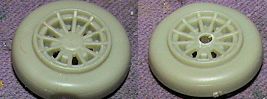
When I got around to assembling
the wheel halves, I found that for both nose wheel options, the area where
the axle fit was not open. I used a drill bit to drill this area out. I also
decided to use the later finned nose wheel as most photos I found of the
F-86D had this wheel, though not all of them so apparently the early wheels
were used until they were no longer viable. These also seem to me to be the
same nose wheels used on the F-80. I found the nose wheel assembly to seem a
bit wide as well. The main wheels are not the finned variety, but the early
'lobed' versions.
Gear wells. Each of the main gear wells is a five piece construct that will
then fit into the lower center fuselage section. Once the wheel wells were
in place, this assembly was set aside. I also finished building up the nose
gear well. I'd determined with some dry fitting that I could install the
nose gear after the well assembly had been finished. When that was dry, the
completed rocket bay was glued to it. I used the lower fuselage section into
which this would eventually fit to be sure that everything was properly
attached.
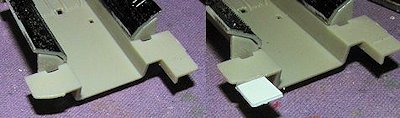
Cockpit. I then moved on to
the cockpit components. I know this is jumping around, but that is often how
I build models. First thing I noticed is that the rear of my cockpit tub was
short shot. Since it was sort of important that this not be like this, I
flattened out the area, cut a section of plastic card to fit in place, and
then attached it. While it was drying, I flooded the underside of it with
super glue as there was a rather large gap that would need to be filled in
somewhat. It is nothing fancy, but does provide the additional bit for when
the tub is installed in the fuselage.
When it came to installing parts G51/52 I found the slots to be too small.
The choice was to thin down the tabs or open the holes. I chose the latter.
You can see the original slots in the above image. I then glued the aft
bulkhead piece after attaching the canopy rails and aft equipment shelf.
Despite the replacement piece, this fit quite well. The seat is very
nicely done, only it is spoiled somewhat by ejector pin marks and some
ejector towers that will have to be removed. Those who build for contests
will have to fill these, but I just left them as they were. I did not
install the head rest or seat pads until after the seat frame had been
assembled and painted. Once all the cockpit and seat frame bits had been
assembled, they were painted dark gull grey. Then the pads were added after
painting them a lighter tan shade. The seat harness was added and the
assembly was set aside.
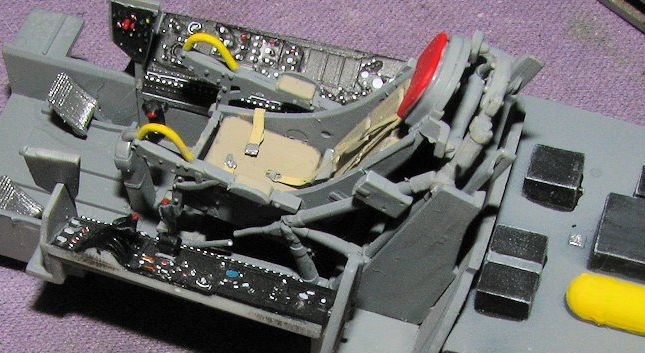
The kit provides
decals for the main side consoles and the instrument panels. These actually
fit over the raised detail, though it took several applications of a strong
setting solution to get them to do so. The end result is quite pleasing. I
then attached all the rest of the bits to the cockpit tub and painted them.
When it came time to install the seat in the cockpit, I found that when I
glued the foot rests in place, it caused the frame to be too narrow for the
openings in the floor. I suggest adding the foot rests after the seat is
installed and before you glue in the control stick.
Once the cockpit was done, it, along with the rocket bay were installed on
the intake section. To this was added the engine (which I did not build up
as you won't see it). The actual mating surface of the engine to
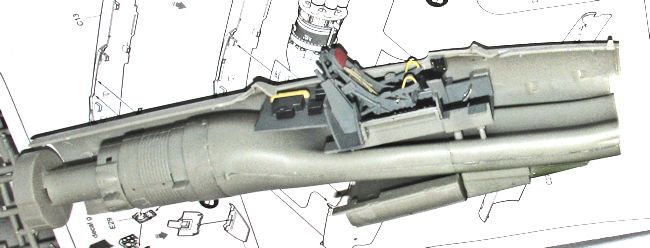
intake section is
quite small so once it is in and glued, I added some reinforcement with
super glue to hold it in place. With that done, this large assembly was
installed in one of the fuselage halves. There are tabs on the cockpit and
engine that will fit into slots in the fuselage half. I did not glue this in
as not only was the fit pretty tight, but I felt that perhaps having some
wiggle room would come in handy later. The other fuselage half was attached,
during which the three piece main instrument panel was also installed. This
installation was less than quick as the small vertical panels that one glues
on each side of the forward cockpit will make installation difficult. I
knocked these off several times before I finally got things in place. This
was followed by gluing on the two lower fuselage sections, the aft one
containing most of the main gear wells. Fit on these was fairly good though
there is a gap between the front and rear lower section that I had to take
care of.
During this assembly, I also glued on the aft bulkhead part D6 as well as
two other bits, D 18 and D 19. The bulkhead is required to keep the forward
fuselage assembly from over-flexing and the two other bits will be needed to
provide an area on which the rear fuselage can sit, otherwise you'll have
little more than a thin butt join. While filling and sanding all the
fuselage seams, I sanded off the TACAN antenna on the nose. These were often
fitted to aircraft operated in the Far East, but not always.
When it came time to attach the forward intake piece, I thought I would have
difficulty with the fit and I was right. Apparently the intake ducting ended
up a bit too far forward for a snug fit. Thanks to super glue and pressure
and filler, I
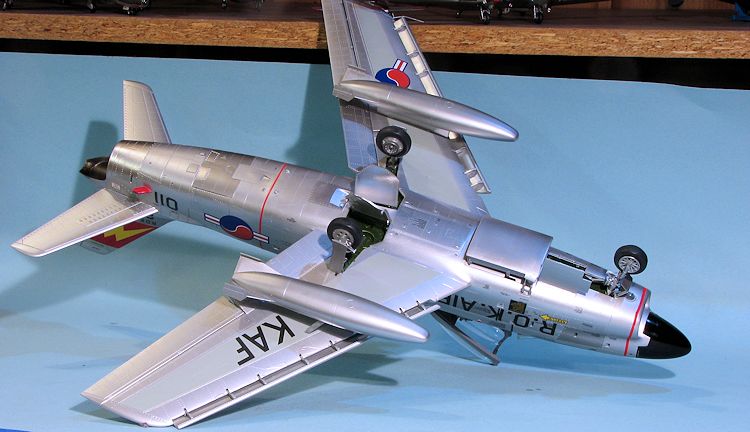
was able to get this piece to look as it should. The rear
fuselage was atrocious. The actual mating surfaces are very thin and if you
make any mistakes in fitting the intake sections (which apparently I did),
the rear will not fit all the way. Thanks to super glue and accelerator, I
was able to squeeze the rear fuselage into some semblance of how it should
fit. I found that the roughly C shaped items attached on the rear fuselage
frame prior to attaching the tail will have to be sanded down to less than
half their thickness to get any resemblance of fit.
Then came the struggle of attaching the wings. The small wheel bay stubs
have an end piece that is too wide to fit into the wings. Not only that, but
the wings themselves make it nearly impossible to slide in place. I had to
open the seams along the flap area in order to spread the wings open enough
to get the stubs in place. Be sure to sand the end of the stubs as well or
you will not get the wings to fit up anywhere close to snugly enough. I also
glued on the fin assembly. All of this took a great deal of super glue to
fill in the various gaps and I had to rescribe the panel lines and
rivet detail lost during all the sanding.
I then attached the tailplanes. Be sure to install them so that the vortex
generators are facing down. At this time, I also decided to have a go at
installing the rocket pod piece. There is a part, C 28, that is shown
fitting to the 'underside' of the rocket bay. If you model this item
extended, that piece should be fairly flush with the underside of the
fuselage. I chose to install that piece before committing the rest of the
tray as test fitting showed it would not fit all the way down. It meant that
I had to trim the long, and easily broken side pieces on parts C10/14, but
was worth doing.
Returning to the wings, I glued on the slats. There are five low ejector
towers on the underside of each slat that will be visible when the slat is
attached so those were sanded down. Only two positive attachment points per
slat are provided, but thanks to the rather soft plastic, getting the slats
in place is a relatively easy job. As a note, it would be a wise move to
attach the slats as soon as you can once you get the wi
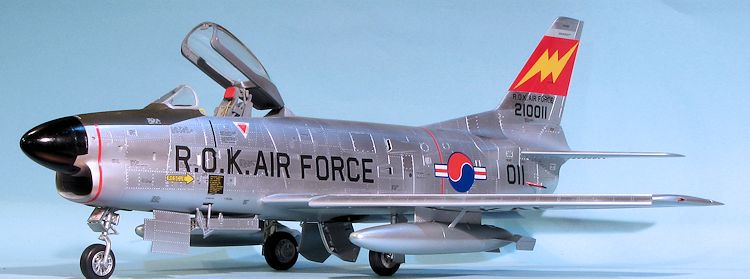
ngs in place. The
reason for this is that the slat track pieces are very easily damaged during
handling and attaching the slat makes things a lot more solid. This was
followed by the installation of the ailerons and flaps.
I then masked and glued on the windscreen. The little back piece to the
canopy was installed along with the piece that attaches it to the airframe.
Note that if you want the canopy closed, you will need to leave this last
bit (G50) off as it is too thick, or you can sand it down. Thanks to the
backward angle of the ejection rail assembly, you will not be able to have
the canopy closed unless you do some major surgery. I then masked the
cockpit section with tissue and tape.
Next, I moved to the landing gear. Be careful not to trim off the mounting
tab on part #G 24 that fits onto the lower nose gear let. I also assembled
the nose gear door. One of my hinges was slightly short shot. When doing the
main gear, in step 16 the upper leg pieces are E 64/65, not 64/68. For the
other side, the two bits are 68/69.
I had been at this a long time and now seemed to be a good time to start
painting. For this, I first sprayed the airframe with Tamiya extra fine grey
primer. When that had dried, I started spraying on Alclad II Aluminum. It
would not be an overstatement to say that not only did this take a long
time, but I went through nearly a full bottle of paint in the process. Many
Sabres had inner wing areas that were painted grey and for mine I chose FS
16473, though I have seen them lighter. This required a lot of masking.
Now a solid aluminum airframe is boring so I used other shades for several
panels including dark aluminum, airframe aluminum, white aluminum,
duralumin and stainless steel. Several of these are rather close to each
other, but the end result is convincing enough. I then masked off the fin
and painted a red band on it using Gunze red over Tamiya white. The nose
anti-glare panel was painted with Tamiya OD. It could be black or medium
green or shades in between. This took a few weeks.
I then painted the gear wells with FS 34102 dark green as that shade looked
similar to what I'd seen in color photos. Next I glued two 14 oz weights to
the area just above the intake to keep the plane from sittin
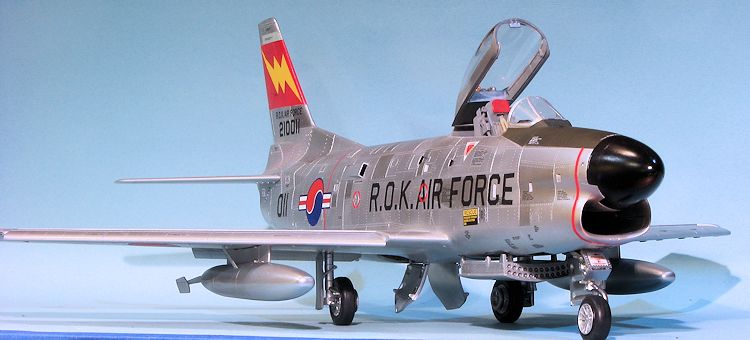
g on its tail.
I had previously assembled the nose and main landing gear and it was time to
install them. The nose gear was pretty straight forward and while snug, did
fit. The main gear, however, needed work. You see, the mounting slots are in
line with the forward and trailing edges of the wing. However, the gear
stubs are straight fore and aft in relation to the axle. Now either I goofed
up when assembling the gear, or there was miscommunication between the team
that designed the main gear wells and those who designed the gear. It is no
irrepairable, just requires some sanding and cutting to get the gear in
place.
Once the gear dried, I attached the small outer gear doors with their
equally small struts. The main gear had the retraction strut attached as
well and things were pretty sturdy. I left off the main nose gear door and
the inner main gear doors as I figured I'd break them during decaling. I
also glued on the radome.
I had chosen the Korean Air Force version as I liked the scheme and didn't
want to do all the additional work to make the others (by that I mean
painting big stripes and bands). The Korean insignia is on a separate sheet
and are printed off register. The white backing peeks out of the lower part
and will need to be trimmed away. Some of the decals conformed beautifully
without any need for setting solution. Most of them, however, required
something relatively strong as weak solutions had no effect. The single
color (as in black) decals are so thin as to be a
bit of a headache to apply as they are constantly wanting to fold and
even if creased will cause issues. Most of the markings are matte, as is
the carrier film, making it difficult to have them disappear against a bare
metal finish.
Putting on the long, skinny markings can be a trial and the large 'ROK AIR
FORCE' markings will be enough to try the patience of Job. You see, these
markings have a thin clear carrier only at the very top and very bottom of
the decal and even then not for the full length of the decal. For instance,
the K is attach
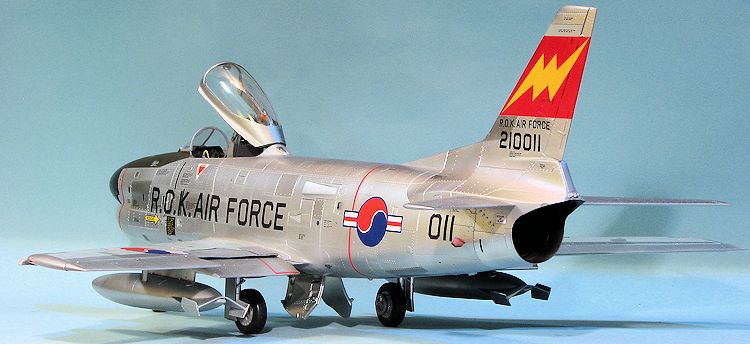
ed to the O and the . in front of it, and the A and . behind
it. The area between the legs has no carrier. This means that the marking is
easily distorted when applying it and requires a lot of fussing to get
straight. This same sort of deal applies to the R, A, F and E with the F and
E having nothing to keep their center bar from easily folding under. This
sort of thing made decal application quite a long and sometimes tedious
affair. I should mention that none of the decals are in segments so you'll
have to cut those if you want open speed brakes or those that go over the
open slats.
Eventually, all the stencils were applied. I found that there were a lot
more on the sheet, but there was no indication as to exactly where these
were to be applied. The sheet also includes only one serial number data
block and that is for aircraft 52-4239 which is none of the markings
options. Interestingly, this airframe is still extant. It was upgraded to an
F-86L and is at the Museum of Flight in Dallas, Texas. For the final
marking, I used a red stripe decal from an old Microscale sheet for the red
stripe on the nose. This decal broke apart several times.